I had a Kip 4 Solenoid Manifold on PS for about 4 years before one of the solenoids started leaking by....Since I have a blowdown system for PS which shares a foam gun with TF, it would eventually allow the hose and gun to freeze even though I have air shutoffs to the flojets. At first, I tried replacing the solenoid plunger even though it looked ok along with the SS seat...It still leaked to the bay...So I ended up putting a whole new manifold in which solved the problem...
After getting it home and taking the manifold apart, I quickly discovered the seat wasn't the issue. The brass between the block and SS base was washed out between the two orings. About .020" deep washout checking it with an indicator....Interesting enough, the manifold didn't leak to the outside, it leaked past the smaller oring towards the center and then to the bay...
I'm sure others have had this issue with washout using PS and brass....But don't throw the block away...It can be skim milled for at least another use...See attached...There was still about .060" clearance after milling at the base of the threaded SS seat and the manifold....Plenty of clearance for flow...
I doubt I put another brass manifold on this function...Actually looking for a SS manifold instead. I found Dema and GC makes one. But pricey at $230+. Does anyone know if Kip has a SS manifold? That way I can at least use the SS Kip parts I currently have....
After getting it home and taking the manifold apart, I quickly discovered the seat wasn't the issue. The brass between the block and SS base was washed out between the two orings. About .020" deep washout checking it with an indicator....Interesting enough, the manifold didn't leak to the outside, it leaked past the smaller oring towards the center and then to the bay...
I'm sure others have had this issue with washout using PS and brass....But don't throw the block away...It can be skim milled for at least another use...See attached...There was still about .060" clearance after milling at the base of the threaded SS seat and the manifold....Plenty of clearance for flow...
I doubt I put another brass manifold on this function...Actually looking for a SS manifold instead. I found Dema and GC makes one. But pricey at $230+. Does anyone know if Kip has a SS manifold? That way I can at least use the SS Kip parts I currently have....
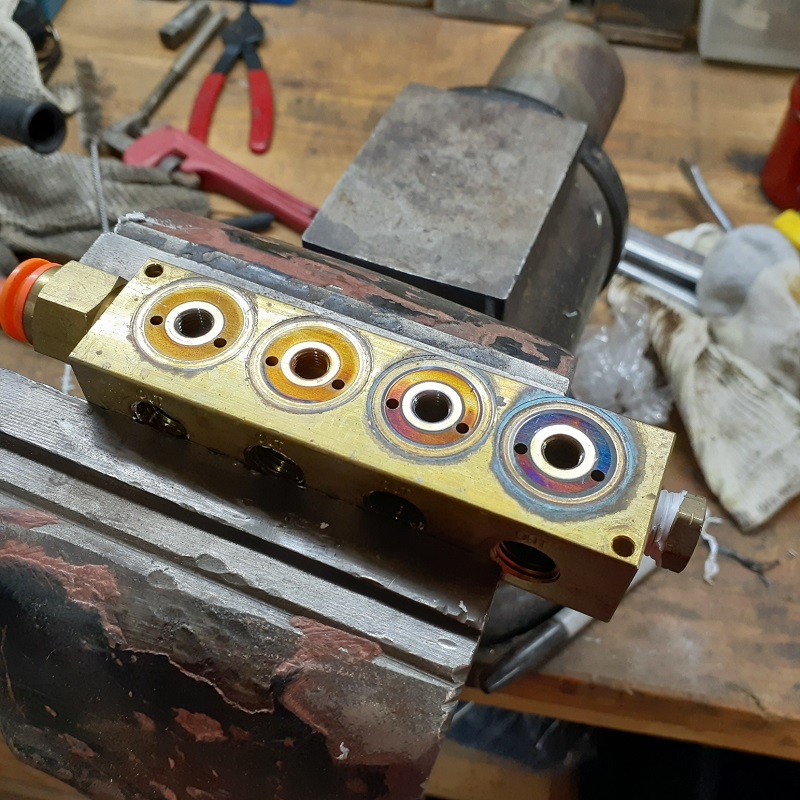
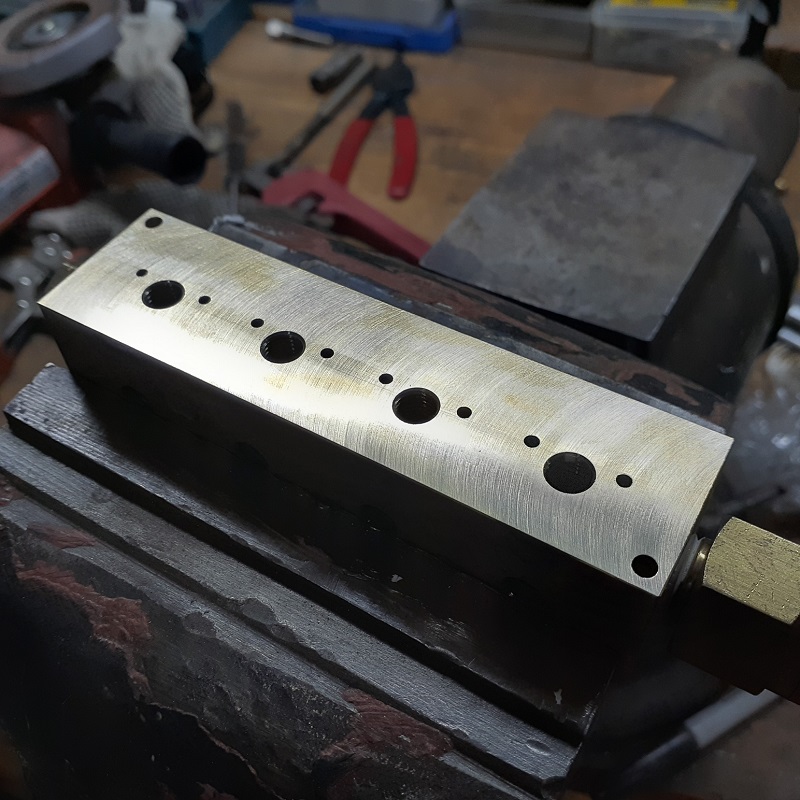